What are Heat Transfer Plates And What Do They Do?
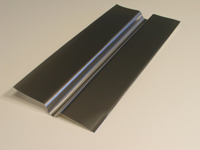
lighter gauge aluminum
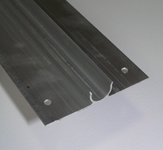
heavy gauge aluminum
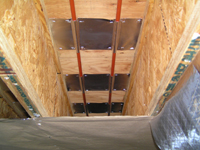
half coverage with aluminum
Heat Transfer Plates are used in so called “staple up systems” where the floor is warmed by placing heating tubes underneath the floor.
Aluminum material wraps around the heating tube and then spreads out and attaches to the under side of the heated floor.
Heat transfer plates perform three important functions.
- They help to carry heat away from the tubing and distribute it through the joist space and along the floor. (Heat transfer)
- They support the plastic heat exchanger tubing.
- They greatly reduce heat loss in the downward direction (backloss).
There are differences of opinion about how much aluminum should be used, how thick it should be and even if aluminum is necessary at all.
Here, we will offer to you the benefit of our research and experience so that you can either understand our recommendation better, or make up your own mind.
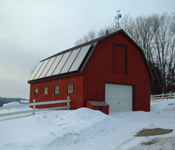
Radiantec Research Facility
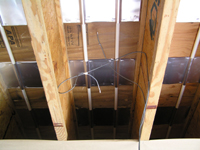
Careful Temperature Measurements
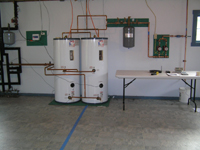
Measuring & Recording Performance
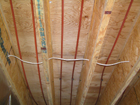
No Aluminum
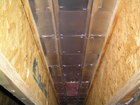
Full Coverage
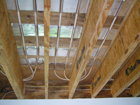
Half Coverage
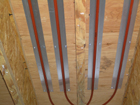
Heavy Duty Aluminum
HEAT TRANSFER – The purpose of your radiant heating system will be to make heat in the form of warm water (in an efficient manner, we hope) and then transfer that heat to your floor. Some process must take that heat away from the tubing and apply it to the underside of the floor so that the floor can heat the area above. Aluminum is a material that transfers heat exceptionally well but it is expensive, and its use should be carefully balanced against other methods of doing the same thing, and its application should be optimized for performance and cost effectiveness.
NO ALUMINUM vs. FULL COVERAGE OF ALUMINUM – Controlled experiments have shown that covering the tubing with medium/thin gauge aluminum plates causes the system to put out about 60% more heat when operated at the same temperature.
If you use no aluminum at all, you must either raise temperature of the fluid in the tubes to a very high level, use more tubing, or both. It is not desirable to operate plastic heat exchanger tubing at high temperatures for reasons of safety, efficiency and service life.
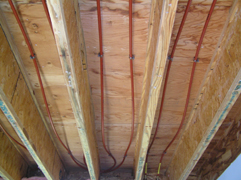
This tubing installed without aluminum plates has developed a sagging problem within a few hours
DIRECTION OF HEAT FLOW – Heat that goes in the wrong direction is called “BACKLOSS”.
The aluminum heat transfer plates have a unique and generally unappreciated property. Aluminum has what is called “low emissivity”. The emissivity of aluminum is .05 vs. .95 for ordinary materials. That means that when aluminum is warm, it emits radiant energy at a much lower rate than most other materials (only 5% as much).
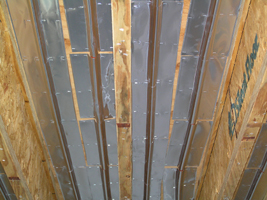
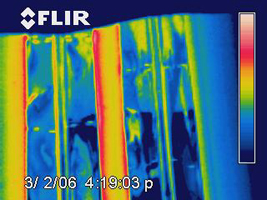
These two images show how aluminum plates can significantly affect the performance of a “staple up” type system.
The image on the left is an ordinary photograph of the underside of a floor that has radiant heating tubes that are fully covered with aluminum heating plates.
The image on the right is an infrared thermograph of the same situation. Yellow and red colors indicate higher emission of heat energy while blue indicates lower emission of heat energy. All materials are about the same temperature in this case (110°F).
SHAPE AND THICKNESS OF THE ALUMINUM PLATE – Aluminum heat transfer plates are available in any number of configurations and a decision must be made about which is ideal. Aluminum is expensive and the cost of installation is important as well. These photographs show some options.
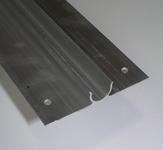
heavy gauge aluminum
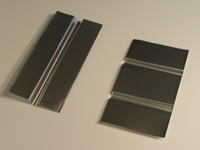
lighter gauge pre-stamped
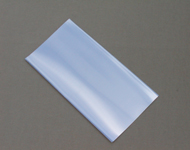
flat stock
A thicker aluminum stock will transfer heat faster than lighter stock. The extruded tubing groove fits tighter to the plastic tube for better contact. Overall, the thicker heavy gauge aluminum plate is 6% more efficient at transferring heat than the lighter gauge pre stamped aluminum plate. However, the heavy gauge material is four times as costly as the lighter gauge material. Also, it must be pre-drilled and screwed to the sub floor and the overall cost is much higher than that of the lighter material. The smaller size means that the low emissivity property of the aluminum will be less.
The lighter gauge pre-stamped material is economical enough to be used more thoroughly. It is thick enough to provide good heat transfer and thin enough to be stapled into place instead of drilling and screwing. The thickness is a little thicker than premium flashing but it is pure aluminum and it undergoes a heat treating process that makes it more malleable (called dead soft) so that it can be worked with easier.
The flat stock is for special applications. The material is malleable enough to be bent into custom shapes.
Heavy duty aluminum foil, available from the supermarket is at the other extreme. However, it is not really thick enough to transmit heat well and is little better than nothing.
RESULTS – Our data suggests that the options of no aluminum plates at all, heavy duty aluminum plates, and aluminum foil can generally be ruled out. The real decision is between a continuous covering of the tubing with a medium/light gauge aluminum stock, or an intermittent covering of half of the tubing. We have arrived at the following recommendations:
If the flooring material is thick or carpeted, the tubing should be covered entirely.
If low operating temperatures are desired, as for solar heating applications or for very high efficiency, or for other reasons, cover the tubing entirely.
Do not hesitate to consult with your Radiantec technician if you have any questions or special applications.