At Radiantec we are committed to research and development that will answer the following important questions about radiant heating design.
- What is the most effective tubing size and circuit length? How does this affect performance?
- Should you use aluminum heat transfer plates? What is the effect on affect performance? How thick should they be?
- How can you maximize heating performance and efficiency?
- How can you lower pumping costs?
- How can you control back losses so that heat goes in the right direction?
The following paper is a summary of findings related to the above questions. More information is available about other radiant heating issues. Do not hesitate to ask your Radiantec technician.
RECAPITULATION OF RESEARCH OBSERVATIONS
MARCH 13, 2007
Description of the project: The project involved the analysis of varying tube and aluminum strategies for radiant underfloor heating as used within floor joists and commonly referred to as the “staple up system“. Heating energy was supplied by a hydronic solar heating system with electric back up for temperature stability.
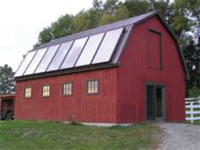
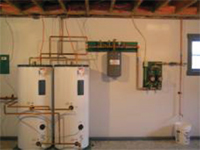
The testing facility was constructed of typical frame construction and was divided roughly in half in order to observe different tubing strategies under equal and identical conditions and make meaningful comparisons between the two without the issues of confounding variables. Heating performance is determined by very careful measurements of water flow and temperature measurements of the water going into and out of the systems.
On the East side of the building, 5/8″ tubing was installed within 16″ joist spaces at spacing of 8″ on center. The tubing was covered to the maximum practical degree with aluminum heat conduction plates. The size was 16″ x 8″ and was variable in thickness and temper.
On the West side of the building, typical 1/2″ Pex tubing was installed at 8″ on center with no aluminum plates at all.
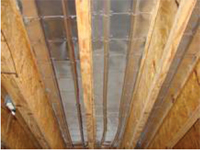
East Side of the Building
5/8″ tubing @ 8″ Spacing
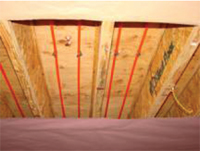
West Side of Building
Typical 1/2″ Pex @ 8″ spacing
Paper backing, with and without out an aluminum foil reflective barrier was installed in portions of the project in order to assess the value of this method in reducing back losses.
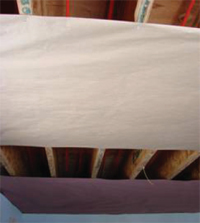
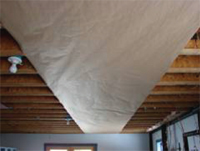
Solar heated water with electric backup for temperature stability was then supplied to both setups simultaneously so that their performances could be directly compared under tightly controlled circumstances.
The water temperatures varied between 146 degrees F and 119 degrees F depending upon the availability of the sun and the adequacy of the electric heating elements to keep up with the workload.
It was possible to draw the following conclusions based upon the above studies.
1. A well designed radiant heating system will minimize what is called “parasitic electric consumption”. This is the amount of electricity that is required to operate the system. Unfortunately, many designers do not care about this important design element and every month, the customer pays more for electricity than he should. Pump work is by far the most important factor. The energy waste is controlled by selecting properly sized tubings and optimizing the length of the circuits. The 5/8″ tubing showed significant advantages in this regard. Common pumps provided identical pumping power to each circuit. The 5/8″ tubing moved significantly more water than the 1/2″ tubing with the same amount of power. The flow rates for the 5/8″ tubings were observed to average 2.15 g/min at the higher temperatures and 2.02 g/min at the lower temperatures. On the other hand, the 1/2″ tubing flowed at only 1.47 g/min at higher temperatures and 1.37 g/min at lower temperatures. Whereas the pumping forces were identical for each situation the superiority of the larger tubing is demonstrated with respect to the efficient utilization of electrical energy to move heated water. The improvement was on the order of a 46% increase in the pumping efficiency. This favorable result is directly related to tubing size and the improved flow characteristics will also translate into the opportunity to specify longer circuit lengths.
2. The aluminum heat conduction plates were shown to be highly effective for two useful purposes.
- In the first instance the aluminum fins worked well in transferring more of the energy available in the heated water out of the tubing. In particular, the aluminum fins placed the heat energy directly on the underside of the floor to be heated whereas the tubing without aluminum fins essentially heated the air in the cavity which was then transferred to the subfloor by the less effective mechanism of convection and conduction of warm air. Heating output in ramp up conditions was observed to be 15,124 btus/hr in the instance of the 5/8″ tubing while the heating output of the 1/2 ” tubing was only 10,955, or an improvement of 38%. At lower temperatures (118 degrees F vs. 145 degrees F), the improvement was less pronounced however and the improvement declined to about 11%. It is necessary to note that the comparisons are not identical because the 5/8″ tubing is slightly larger than the 1/2″ tubing, but other studies that contrasted the tubings alone suggest that the positive results are mainly attributable to the aluminum.
- Another very important factor in the design of radiant heat is the control of so called “back losses” which is heating energy that goes in the wrong direction. Those who would say that heat loss downward is not relevant because heat always rises are misinformed. The joisted floor application does indeed control heat loss by convection and conduction to near zero in a natural and effective manner. However, radiant heat is capable of going in all directions.
Practical experience and these data strongly indicate that if radiant heat loss in the downward direction is not controlled well, the results will be unsatisfactory. When heat loss goes in the downward direction to another heated space, that heated space can actually be overheated while the intended space is inadequately heated. These data strongly suggest that most of the heating energy supplied by the 1/2″ PEX tubing without aluminum fins is going in the wrong direction. This is a situation that must be corrected with the added expense of some type of additional insulation. Unfortunately this remedial action often does not take place.
An under appreciated benefit of the aluminum conduction fins is its low emissivity (nearly zero). This means that when aluminum is warmed, it does not emit radiant energy to the extent that other materials do. In the current instance, this property is put to good use to control the radiant “back losses” which would seriously impair the system if not controlled. The superior effect of the low emissivity is clearly demonstrated by infrared thermographs which show nearly no radiant heat losses downward when the aluminum is used.
In particular, the thermograph (below and left) is instructive. The infrared camera only “sees” the radiant heating spectrum and then makes a mathematical correction to predict the molecular temperature based upon the radiance measured. This method works fairly well with nearly all materials, but aluminum an exception. It is seen that the aluminum conduction fins are colored blue in the thermograph, falsely reporting that it’s temperature is only 67 degrees when in fact, it is actually 106 degrees. It is noteworthy that the actual infrared energy emitted by the aluminum is nearly zero. The camera is recording reflected radiation from the environment below. These effects reduce back losses of the aluminum from radiance to nearly zero.
Aluminum fins contain radiant heat loss and are actually at 106 degrees here.
Radiant Heat is lost without Aluminum Fins. Such backloss should be avoided.
- Another useful property of aluminum is the fact that it reflects radiant energy which strikes it from another source. An additional sheet of aluminum foil placed underneath the radiant floor will act to reflect any radiant energy that is going in the wrong direction. Fortunately this property can be had with extremely thin aluminum foils that are commonly bonded to reinforced paper for strength. The value of the foil faced reflective barrier is clearly demonstrated in the work. Radiant energy that would other wise be misdirected as backloss is reflected upwards to the subfloor where it is useful to the occupant. The infrared thermographs clearly show the improvement of the foil backed material when compared directly to ordinary paper.
Flir Research with paper backing
Flir Research with paper backing
It is evident that ordinary paper is nearly useless in retarding back losses whereas the reflective barrier is effective in reflecting much of the heat that would otherwise be lost. In the thermograph (above right), the material covering the floor joist on the left is aluminum foil backed paper. Its temperature is 64 degrees F. The shorter length of material on the right is ordinary paper without a foil facing. Its temperature is 68 degrees F. This is a considerable difference.
CONCLUSION
The cumulative effect of these phenomena is clear from the following thermograph.
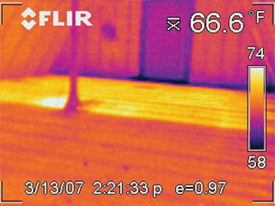
Attention to Detail improves Efficiency & Performance
Attention to detail has produced a large improvement in both the efficiency and performance of the radiant heating system.
The heating output of the tubing with aluminum conduction fins is vastly superior to the tubing that lacked aluminum conduction fins. In addition, without extra insulation efforts, what little heat will be released by the tubing alone is going to go in the wrong direction. Aluminum is a unique material with some unusual and highly desirable properties. The performance of relatively thin aluminum stock was compared with thicker stock. Expense and workability issues favor a broader coverage with the thinner stock instead a more limited coverage with thicker stock.
The temperature of the floor with the 5/8″ tubing averages 71.5 degrees F whereas the temperature of the tubing without plates averages only 66.8 degrees. This 5 degree difference is enormous within the context of a radiant heating system.
In most cases, it will be the difference between a successful project that delivers the heating energy that is required with the high efficiency that our customers have the right to expect and a project that underperforms and is less efficient than other forms of heating.
The heating output of the 5/8″ PEX design with aluminum conductions fins is 58.5 BTUs per square foot of floor area when operated at 146 degrees F and nearly all of this heat is going up where it is supposed to go. The 1/2″ PEX design without aluminum fins puts out only 72% of this amount, and the majority of the heat is wasted backloss.
There are significant safety and service life advantages to the system owner in terms of high performance at reasonable temperatures. In addition, reasonable operating temperatures can facilitate the use of alternative energy sources such a solar.
IMPORTANT NOTE: This report in no way disparages the use of 1/2″ PEX as a material for use in radiant heating systems. The problems that we mention can often be solved by other means. Our goal here is to illustrate some important issues in the staple up systems and increase customer knowledge and satisfaction.
It is, however our express intention to point out serious problems that do exist in theory and in practice with staple up systems that do not use aluminum conduction fins and make inadequate provisions to control back losses.
Additional links and resources:
DOE Solar Report – This report describes very high efficiency in a simple solar heating system that uses a radiant heated slab for both heating and energy storage. The unusually high efficiency is the result of the uniquely low operating temperature of the radiant panel slab. The performance of the heat exchanger tubing is evaluated and optimized for both efficiency and parasitic electrical consumption.
ASES Paper – This paper is a 3 page excerpt of the above Department of Energy Report and was presented to the International Solar Energy Association at their 1984 meeting.
Copyright, Robert J. Starr 2007